Barcodes in Manufacturing
Barcodes are essential tools in modern manufacturing. They streamline operations, improve accuracy, and enhance traceability throughout production. These identifiers are used in many stages of manufacturing, from inventory management to quality control. By using barcodes, manufacturers can create efficient, accurate processes that increase productivity and reduce waste.
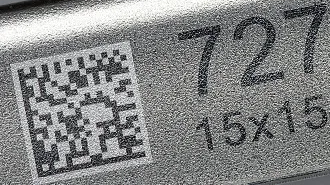
Barcode technology in manufacturing offers many benefits beyond simple identification. It allows real-time tracking of materials and products, enables data collection and analysis, and provides quick, accurate item identification. This precision and control is crucial in industries with strict regulations and safety requirements, such as pharmaceuticals and food production. In these sectors, detailed record-keeping and product tracing are vital for public health and safety.
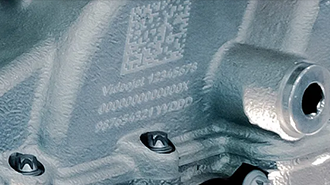
Barcodes connect physical items to digital systems, allowing manufacturers to keep accurate, up-to-date records easily. This integration improves efficiency and provides valuable insights that can drive improvement and innovation in manufacturing processes. By using barcode technology, manufacturers can stay competitive in today's fast-paced market, meeting customer expectations while following industry standards and regulations.
_2068412296.webp)
Inventory Management
Barcodes are key tools for tracking materials and managing inventory in manufacturing. They let manufacturers monitor stock levels in real-time, giving a clear picture of available resources. This helps avoid running out of stock or having too much inventory, which can both cost money.
Barcode technology does more than just track items. Using barcode scanners, manufacturers can update inventory counts automatically. This is faster and more accurate than manual data entry.
Barcodes also track materials as they move through production. This helps manufacturers know where each item is at any time. This information can improve production schedules, reduce waste, and make operations more efficient.
When combined with inventory management software, barcodes enable advanced inventory control methods like just-in-time (JIT). These methods help keep costs down while ensuring materials are available when needed for production.
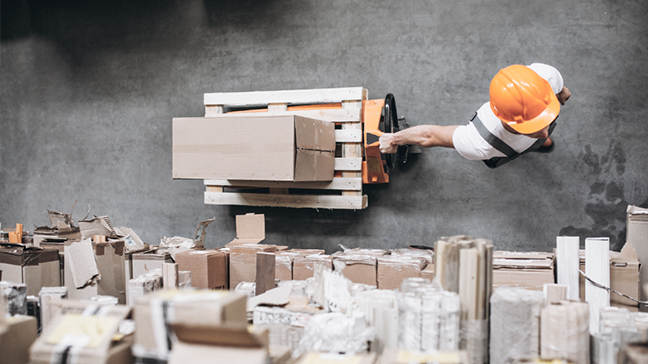
Production Line Efficiency
Barcodes are essential in manufacturing, revolutionizing item tracking throughout production. They provide real-time visibility into production, eliminating delays and errors. This advanced tracking ensures the use of correct components at every step, maintaining product integrity and quality. One particularly important type of barcode in manufacturing is the Direct Part Marking (DPM) barcode.
DPM barcodes are etched or engraved directly onto parts and components, making them ideal for industries where traditional labels may not survive harsh manufacturing processes. These durable barcodes are widely used in automotive, aerospace, and electronics manufacturing, where part traceability is crucial throughout the product lifecycle.
The implementation of barcode technology, including DPM, in manufacturing significantly reduces rework. By providing accurate, real-time data across the production line, manufacturers can quickly identify and resolve issues. This proactive approach saves time and resources while maintaining high product quality. The precision of barcode data enables rapid decision-making and immediate interventions, streamlining the production process.
Beyond reducing errors and rework, barcode-based tracking systems enhance overall production line efficiency. They allow manufacturers to optimize workflows precisely, identifying bottlenecks, improving resource allocation, and balancing workloads across production stages. This deep insight into the manufacturing process empowers managers to make confident, data-driven decisions, fostering continuous improvement in productivity and output quality.
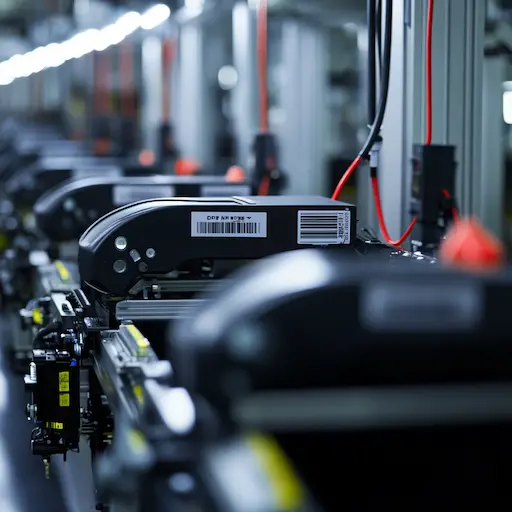
Quality Control
Barcodes are key for quality control in manufacturing. They track batches and lots precisely, which is crucial for industries like pharmaceuticals and food production that have strict quality rules. This tracking helps manufacturers keep detailed records of materials, processes, and products, meeting regulations and quickly addressing quality issues. This makes it easier to find and isolate faulty products. If there's a quality problem, manufacturers can trace affected items to their source quickly, pinpointing the exact batch or lot. This precise tracking helps limit recalls and efficiently find and fix the causes of quality issues.
Inspectors can scan barcodes for instant access to quality details, history, and item specifications. This quick access to important information helps make better decisions during quality checks and maintains consistent quality across production runs.
The traceability from barcode systems helps maintain high quality standards over time. By analyzing data from barcode scans, manufacturers can spot trends, patterns, and areas to improve in their quality control. This data-driven approach to quality management allows for ongoing improvement of manufacturing processes, leading to better product quality and fewer defects.
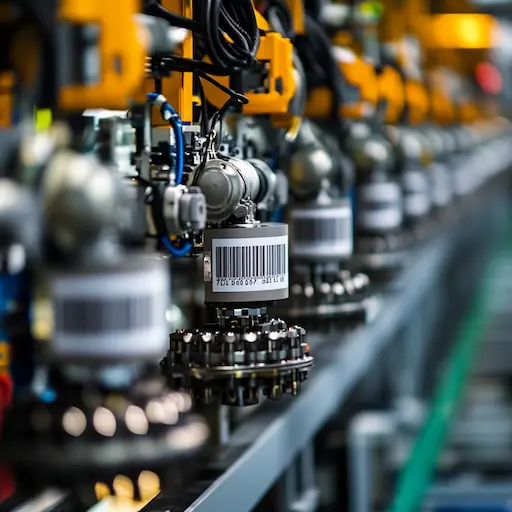
Asset Management
Manufacturers use barcodes for asset management, mainly to track and maintain tools and equipment needed for production. They give each piece of equipment a unique barcode. This lets them check availability, location, and status quickly. As a result, tools are easy to find when needed, which reduces delays and improves resource use across production areas.
Barcodes also help create detailed maintenance records for each piece of equipment. Scanning a barcode shows important information like maintenance history, upcoming service dates, and how to use the equipment. This quick access to data helps prevent breakdowns and production stops by allowing for proactive maintenance.
When combined with asset management software, barcode systems enable predictive maintenance. By looking at data from barcode scans, manufacturers can spot patterns in how equipment performs. This helps them catch potential issues early. Such an approach prevents unexpected downtime and makes equipment last longer, leading to smoother operations and better overall equipment effectiveness (OEE).
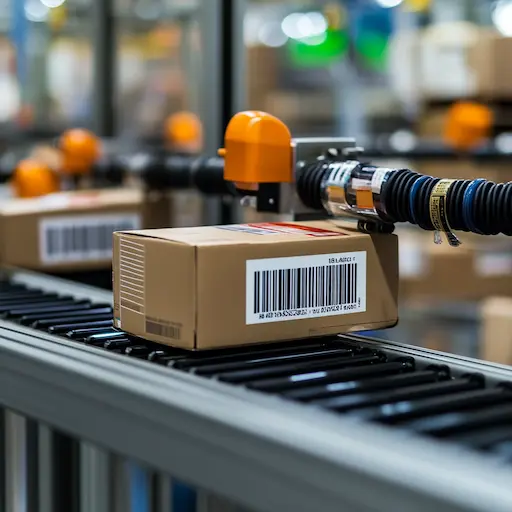
Traceability and Compliance
Tracking and following rules in manufacturing is greatly enhanced by barcodes. These digital tools help create detailed records of production, which are needed to meet strict regulations in many industries. By using barcodes, manufacturers can record every step from raw materials to finished products, making a complete trail for audits.
When a product needs to be recalled, barcodes prove especially useful. They allow manufacturers to quickly find affected products, tracing them back to specific batches, dates, or even individual parts. This fast identification is important for targeted recalls, reducing the impact and scope. By finding exactly which products need to be removed, manufacturers can act quickly to keep consumers safe and limit damage to their finances and reputation.
The benefits of barcodes extend beyond recalls. They demonstrate that manufacturers are following industry rules, quality standards, and safety procedures. This is very important in strictly regulated industries like medicine, food, and aerospace, where proving where products come from and how they were made is often required by law. With barcodes, manufacturers can easily show regulators the required documents and proof of compliance, making audits and inspections smoother.
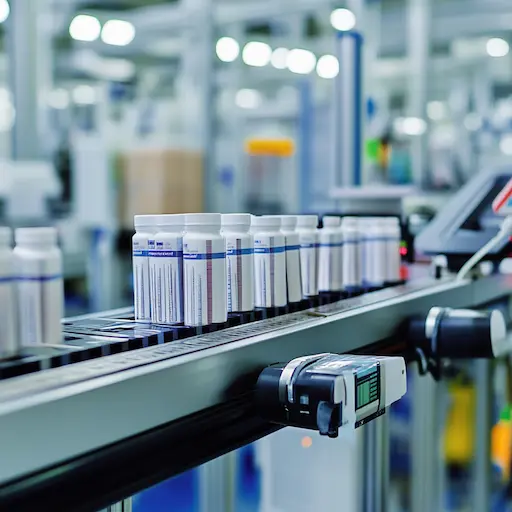
Shipping and Logistics
Barcodes are vital for improving shipping and logistics in manufacturing. They track finished goods from packaging to delivery, making distribution more efficient and accurate. Shipping labels with barcodes contain key information like destination, contents, and handling instructions. This data helps reduce errors during transportation.
Using barcodes in shipping and logistics has clear benefits. It cuts down on misrouted or mishandled products by allowing quick scans at checkpoints. Manufacturers can always see where their inventory is and its status. Barcodes also make order fulfillment more accurate, as warehouse staff can easily find and confirm the right items for each shipment. This means fewer wrong deliveries.
Barcodes speed up processing for outgoing and incoming shipments. They automate data capture, removing the need for slow manual data entry. This speeds up the whole logistics process. Faster and more efficient shipping leads to happier customers through quicker deliveries and fewer errors. In the end, using barcodes in shipping and logistics makes operations smoother and supply chains more responsive and reliable. This gives manufacturers an edge in today's fast-moving market.
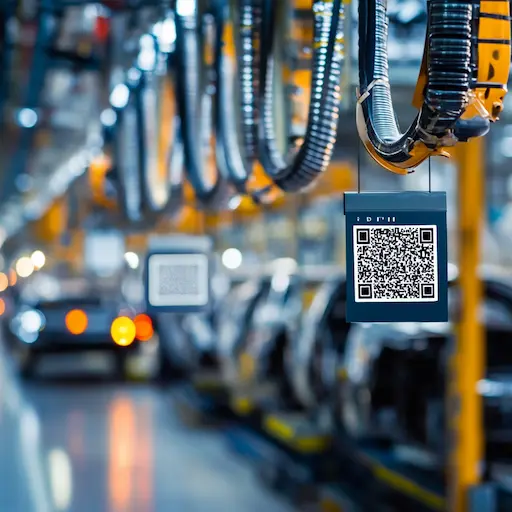
Data Collection and Analytics
Barcodes serve as a rich source of data, offering manufacturers deep insights into various aspects of their operations. This valuable information enhances production efficiency by helping identify bottlenecks, optimize workflows, and boost overall productivity. It also provides detailed insights into equipment usage patterns, enabling better maintenance scheduling and resource allocation. Moreover, barcodes allow for precise tracking of inventory levels, giving real-time visibility into stock availability and movement.
The wealth of data generated by barcode systems supports comprehensive operational insights. Manufacturers can analyze trends, patterns, and anomalies in their processes, leading to more informed decision-making and continuous improvement initiatives. This data-driven approach extends to demand forecasting, where historical data combined with current market trends can be used to predict future product demand more accurately.
By harnessing these insights, manufacturers can significantly enhance their production planning processes. They can align production schedules with anticipated demand, optimize resource allocation, and minimize waste. This level of precision in planning leads to more efficient operations and better utilization of resources. Furthermore, the data supports more effective inventory management, allowing manufacturers to maintain optimal stock levels, reduce carrying costs, and improve cash flow.
In essence, the data collected through barcode systems transforms into a powerful tool for strategic decision-making, operational excellence, and competitive advantage in the manufacturing sector.
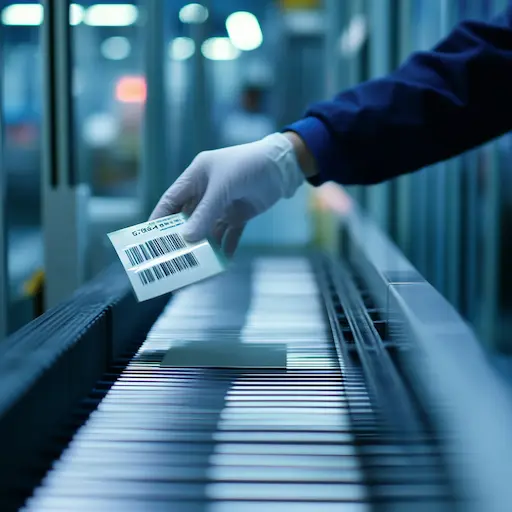
In a nutshell - Benefits of Barcodes in Manufacturing
- Accuracy: Barcodes minimize human error in data entry and product handling.
- Efficiency: They accelerate processes like inventory counting, order fulfillment, and shipping.
- Cost-Effectiveness: Barcodes automate routine tasks, reducing labor costs and increasing productivity.
- Traceability: They enhance the ability to track products throughout the supply chain, from raw materials to finished goods.
- Compliance: Barcodes help manufacturers meet industry standards and regulatory requirements, ensuring quality and safety.
Main barcode types used in manufacturing
Code 128
Overview: Code 128 is a high-density linear barcode that can encode a large amount of data in a compact space. It's widely used in manufacturing for tracking parts, components, and products throughout the supply chain.
Applications:
- Inventory Management: Ideal for labeling raw materials and finished goods.
- Shipping Labels: Frequently used on shipping labels to provide detailed information about packages.
- Work-in-Progress (WIP) Tracking: Helps monitor the progress of items on the production line.
Data Matrix
Overview: Data Matrix is a two-dimensional (2D) barcode that can store large amounts of data in a small area. It's highly resilient to damage and distortion, making it ideal for marking small items and components.
Applications:
- Component Marking: Commonly used to mark small electronic parts, medical devices, and aerospace components.
- Traceability: Enables detailed tracking of items through the manufacturing process, ensuring compliance with regulatory standards.
- Direct Part Marking (DPM): Often used for direct part marking, where the barcode is etched or engraved directly onto a product.
QR Code
Overview: QR Codes are another type of 2D barcode, capable of storing both alphanumeric and binary data. They are versatile and can be scanned easily by a wide range of devices, including smartphones.
Applications:
- Asset Management: Used for tracking tools, machinery, and other assets within a manufacturing facility.
- Product Information: Can link to online databases, providing detailed product information, instructions, or safety guidelines.
- Maintenance Records: Often used on equipment to link to maintenance logs and schedules.
UPC (Universal Product Code)
Overview: UPC is a widely recognized linear barcode, primarily used in retail but also in manufacturing for tracking consumer goods.
Applications:
- Finished Goods Labeling: Used to label products that are ready for retail, ensuring they can be easily scanned at the point of sale.
- Inventory Tracking: Helps in tracking large volumes of consumer products through the supply chain.
PDF417
Overview: PDF417 is a stacked linear barcode that can encode a significant amount of data, including text, numbers, and binary information. It is particularly useful for applications requiring detailed information.
Applications:
- Shipping and Receiving: Used on shipping labels and packing slips to encode complex information like destination addresses and itemized lists.
- Compliance Documentation: Often used to store legal and compliance documentation directly on a product or its packaging.
Code 39
Overview: Code 39 is one of the oldest barcode types still in use, known for its simplicity and ability to encode both letters and numbers. It's widely used in manufacturing for general labeling purposes.
Applications:
- Part Identification: Used for labeling parts and components, especially in automotive and aerospace industries.
- Inventory Control: Commonly used in inventory systems to track items within a warehouse or production facility.
- Work Orders: Often included on work orders and job cards to track tasks and materials.
How can barKoder SDK help you?
The barKoder SDK excels at reading DPM barcodes, which are heavily used within the manufacturing industry, in fact, reading these barcodes is one of the strong points of the barKoder SDK, further more with the exceptional algorithms like Segment Decoding or Matrix Sight we add even more value to your barcode scanning solutions.
barKoder Features related to manufacturing
- Color and Contrast: Direct Part Marking (DPM) barcodes, etched into surfaces, often struggle with contrast. As the barcode color matches the surface it's etched on, shadows can create variations in contrast—making decoding a challenge.
- Dots Instead of Lines: DPM uses dots instead of lines found in regular barcodes. The distance between dots and their shape greatly impact how well the code can be read. If dots are too close or too far apart, it can cause reading errors. Oddly shaped dots make it even harder to scan correctly.
- Surface Imperfections: Surface texture affects DPM etching quality. Reflective, uneven, or curved surfaces, along with damage or abrasions, can make scanning difficult. These surface imperfections directly impact the readability of the code.
- Challenges in Lighting: DPM barcodes are often found on curved metal surfaces and may not have ideal contrast under ambient lighting conditions. The placement of DPM barcodes in areas with poor lighting can introduce additional challenges for decoding.
- Reliability in Confined Spaces: In electronic manufacturing, DPM codes can be particularly challenging due to their low contrast and tiny size, as they are directly printed on electronic components. Reliably reading such codes is crucial.
As mentioned before, customers can utilize our special features like:
to maximize their ability to use barcodes within their healthcare solutions.
If you want to improve your operations with barKoder SDK, our documentation has everything you need to add our barcode scanning tech to your systems. For technical details and setup guides, check our documentation page.
Get started by requesting a quote. Our team will show you how barKoder can boost your inventory management, speed up checkouts, and provide key business insights using advanced barcode technology.