The Role of Barcodes in Modern Logistics
Barcodes play an essential role in streamlining logistics operations by enabling real-time tracking, accurate inventory management, and efficient data collection. From the moment goods enter a warehouse to the point they reach the end consumer, barcodes help maintain transparency and accuracy at every step. Below are key areas in logistics where barcodes prove indispensable, followed by some of the most commonly used barcode types.
Inventory Management
Barcodes are fundamental to tracking inventory in logistics. Similar to their use in retail, each product or package is labeled with a barcode that holds critical information—such as product ID, quantity, and location. When scanned, the system updates in real time, offering a clear picture of stock levels and movements.
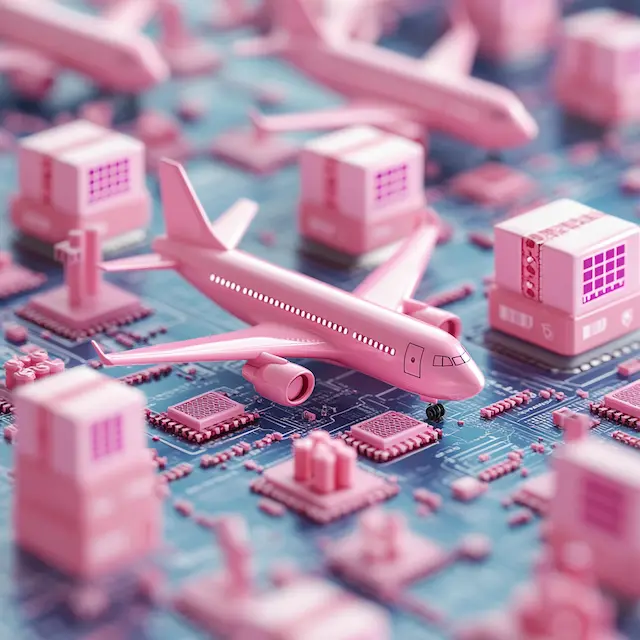
By automating data capture, logistics companies avoid manual record-keeping errors and maintain more accurate inventory counts. This reduces discrepancies, minimizes stockouts or overstocks, and helps streamline reordering. The end result is improved warehouse efficiency and better customer satisfaction due to timely order fulfillment.
Scenario:
Throughout the day, products are moved from storage racks to packing stations. Staff use handheld scanners to record each movement by scanning barcodes on products and shelving units.
Outcome:
- The inventory management system automatically updates, so you always know exactly how many units remain in each location.
- Real-time data reduces stockouts and overstock situations, helping you reorder the right amount of inventory at the right time.
- Management gains up-to-date insights into stock levels, simplifying decisions on reordering, shipping schedules, or promotional planning.
Receiving and Putaway
Upon arrival at a warehouse or distribution center, barcodes on incoming goods are scanned to verify that the shipment matches accompanying documentation. This verification process ensures the correct items have been received. The system then guides workers on where to store each item, a process known as “putaway.”
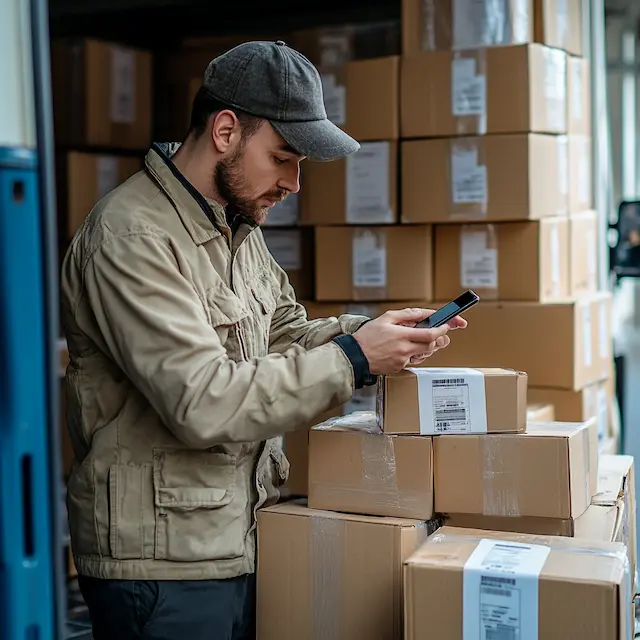
Scenario:
A delivery truck arrives at your warehouse with multiple pallets of goods. Each pallet has a barcode label indicating its contents (item IDs, quantities, and destination aisle). Upon arrival, a receiving clerk quickly scans each barcode.
Outcome:
- The system verifies that the received goods match the purchase order, instantly updating inventory counts.
- Warehouse staff see where items should be stored or “put away” (e.g., shelf location), speeding up the entire intake process.
- Any discrepancies (like missing items) are flagged immediately, reducing mistakes and saving time later.
Order Picking
Accurate order picking is critical to meeting customer expectations. Barcodes simplify this process by directing warehouse staff to the exact location of each required item. When workers scan the barcode on a product, the system confirms they have picked the correct item and updates inventory levels in real time.
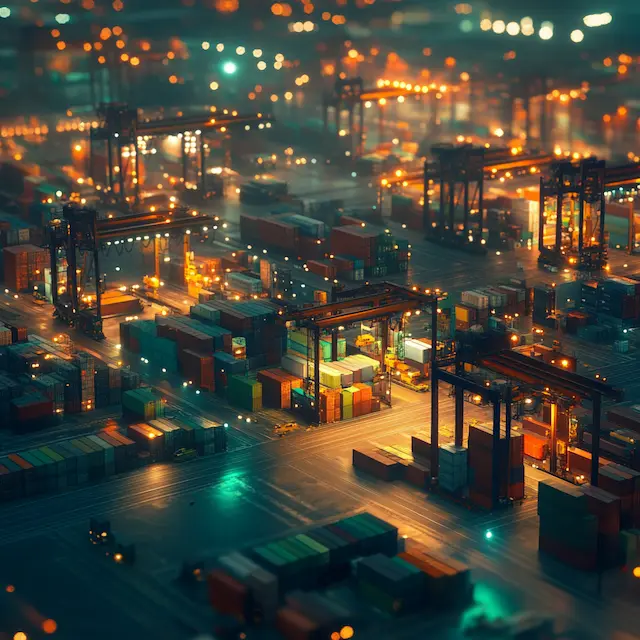
This level of accuracy helps reduce mis-picks, lowers return rates, and improves overall customer satisfaction. It also increases productivity, as workers can quickly move from one pick to the next without manual cross-checks.
Scenario:
A customer places an order for multiple items stored in different areas of the warehouse. A picker receives a digital pick list on a handheld scanner, which directs them to specific storage locations.
Outcome:
- The worker scans each item’s barcode to confirm they’ve picked the correct product.
- Any errors (like picking the wrong item) are immediately flagged, preventing shipment mix-ups.
- This process increases order accuracy, boosts customer satisfaction, and saves on return shipping costs.
Packing and Shipping
Once items are picked, barcodes continue to play a key role in packing and shipping:
- Packing Verification: Scanning barcodes during packing ensures the correct items are grouped together, reducing the likelihood of shipping errors.
- Shipping Labels: Barcodes on shipping labels contain essential details for transit, including destination and tracking information.
- Real-Time Tracking: Every scan—from packing to final delivery—is logged, enabling accurate, up-to-the-minute package tracking for both the logistics company and the customer.
This end-to-end visibility greatly enhances transparency, building trust with customers who appreciate real-time status updates on their orders.
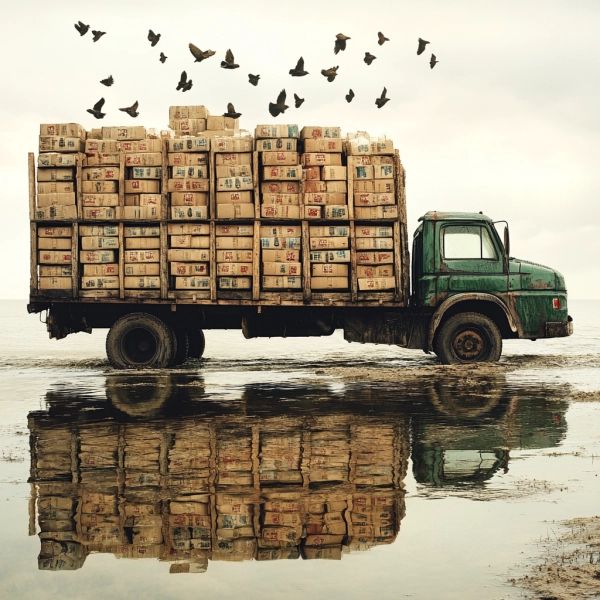
Scenario:
After items are packed, a shipping label—also bearing a barcode—is generated. Before sealing each box, a staff member scans the shipping label.
Outcome:
- The system confirms that the items in the box match the order details, preventing shipping mistakes.
- Tracking information is linked to the shipment in real time, allowing customers (and your team) to monitor the package’s journey.
- Errors like sending the wrong box to the wrong address become far less common, reducing reshipping costs and customer complaints.
Tracking and Tracing
Barcodes empower logistics teams to track goods at each checkpoint in the supply chain. Whether an item is in transit, at a sorting center, or out for final delivery, scanning its barcode logs its exact location.
Consequently, companies can proactively address bottlenecks or delays, ensuring a smoother experience for customers and partners alike.
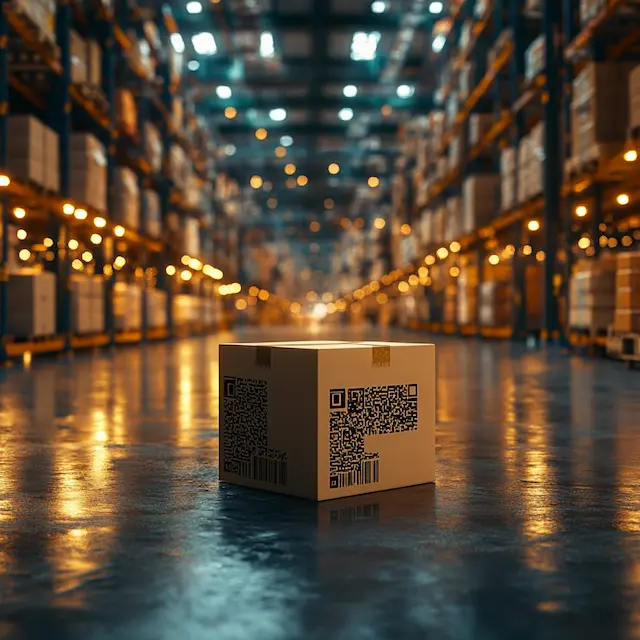
Scenario:
An e-commerce company ships a high-value electronic item from its distribution center to a customer in another country. Every parcel carries a barcode label that includes the product ID, shipment details, and destination.
Shipping Origin Scan
- Once the item is packaged, warehouse staff scan the parcel’s barcode. This confirms in the system that the item has left the distribution center.
- The system automatically updates the shipping manifest and generates a real-time status for the customer: “Order Dispatched.”
Transit Checkpoints
- As the parcel travels from one shipping hub to another (e.g., airport cargo facilities or regional depots), each hub scans the barcode upon arrival and departure.
- These scans update the central tracking system, which in turn notifies both the logistics team and the customer where the package is at any given moment.
Customs Clearance
- When the parcel arrives at the customs checkpoint in the destination country, it’s scanned again.
- The system logs that the item is undergoing clearance, providing visibility into potential delays. If customs requires documentation, the shipping provider can quickly retrieve all the relevant data linked to that barcode (such as declared value, origin, and contents).
Local Delivery Depot
- After clearing customs, the parcel arrives at the local delivery depot, where it’s scanned yet again.
- This action triggers the next customer notification: “Package Arrived at Local Facility,” and allows the logistics team to plan the final delivery route efficiently.
Final Delivery
- A delivery driver scans the parcel upon loading it into the delivery vehicle.
- Upon successful delivery, the driver scans the barcode one last time, marking the order as “Delivered” in the system.
Outcome:
- End-to-End Visibility: Both the customer and the logistics company have real-time data on the parcel’s location and status.
- Issue Resolution: If the package goes missing at any checkpoint, the last recorded scan provides a clear trail to investigate.
- Reduced Customer Inquiries: Automatic status updates lower the volume of “Where is my package?” questions, freeing customer support to focus on more complex issues.
- Improved Efficiency: Knowing exactly where each parcel is at all times helps logistics managers optimize routes, anticipate bottlenecks, and communicate more transparently with all stakeholders.
Returns Management
Returns are a natural part of the logistics cycle, and barcodes simplify the entire reverse logistics process. When a return is initiated, scanning the product’s barcode retrieves all necessary details, such as original order information and reason for return. This allows for:
- Efficient Processing: Quickly update inventory records and determine the next steps (e.g., restock, repair, or discard).
- Streamlined Refunds/Replacements: Ensures prompt issuance of refunds or replacements, improving customer satisfaction.
Barcodes also help track the status of returned items throughout the reverse logistics process, aiding in better record-keeping and inventory control.
Scenario:
A customer initiates a return. The returned product arrives back at the warehouse with a barcode label that ties it to the original order.
Outcome:
- Scanning the barcode instantly retrieves purchase history, reason for return, and any special instructions for restocking or disposal.
- This speeds up the inspection and restocking (or refurbishing) process, allowing for quick refunds or replacements.
- Detailed records help identify frequent return patterns, offering insights into product quality issues or packaging improvements.
Data Collection and Analysis
Each barcode scan generates valuable data on product movements, inventory levels, and operational flow. Overall, barcode-driven data analytics turn raw information into actionable strategies, helping logistics operations stay competitive and customer-focused. Let's look at the following use case.
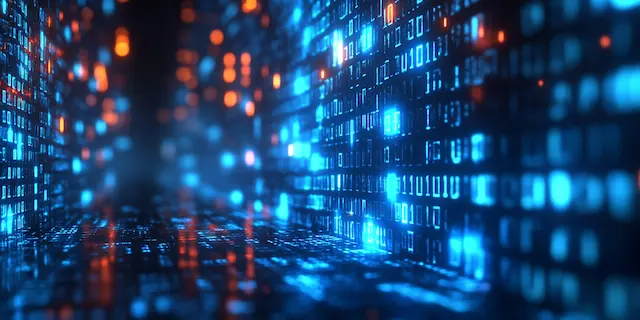
Scenario:
A mid-sized logistics company implements a centralized system that captures every barcode scan throughout its supply chain. Each time a product is received, put away, picked, packed, or shipped, relevant data points—such as timestamps, product details, and location—are recorded in a database.
Comprehensive Data Capture
- Barcodes on individual items, cartons, or pallets are scanned at each key stage (receiving, warehouse movement, shipping, etc.).
- These scans generate high-granularity data, including item ID, movement time, and storage location.
Consolidation into a Central Repository
- All barcode events automatically feed into a central data warehouse or cloud-based analytics platform.
- The system aggregates information from multiple facilities, providing a single source of truth for the entire operation.
Trend Analysis & Forecasting
- Managers use BI (Business Intelligence) tools to create dashboards showing shipment volumes by day, week, or season.
- Machine learning models analyze historical data to forecast peak shipping times, helping the company plan labor and transportation resources more accurately.
- Inventory planners identify the most frequently moved items, adjusting reorder levels to prevent stockouts or overstocks.
Bottleneck Identification
- By reviewing average dwell times at each stage, the logistics team can see where delays most often occur (e.g., receiving dock, packing station, or dispatch area).
- Detailed insights help them optimize workflows, such as adding more staff during peak hours or reorganizing warehouse layouts to reduce travel time.
Continuous Improvement
- When shipping inaccuracies or bottlenecks are found, managers drill down into the barcode logs to pinpoint root causes (e.g., repeated errors at a specific scanning station or during certain shifts).
- Corrective actions—like retraining staff, updating SOPs, or adjusting shift schedules—are then implemented and tracked.
Real-Time Monitoring
- Operations supervisors can view live dashboards that reflect current warehouse activity, giving early warnings if items are stalled or if certain zones are overloaded.
- Immediate visibility allows for quick re-routing of labor or changes to picking priorities.
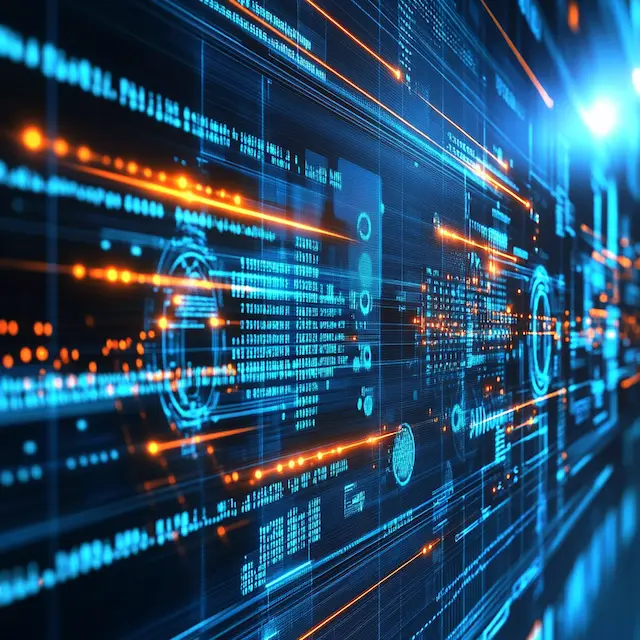
Outcome:
- Data-Driven Decision-Making: The organization moves away from guesswork and relies on concrete metrics to optimize everything from staffing to inventory levels.
- Improved Efficiency: Historical trends and real-time alerts help minimize delays and reduce errors, resulting in faster, more reliable shipments.
- Cost Savings: Better forecasting and streamlined processes often translate into lower labor costs, reduced waste, and higher overall profitability.
Compliance and Security
In industries with strict regulations—like pharmaceuticals or food logistics—barcodes facilitate full traceability. Each product’s journey through the supply chain is logged, helping companies comply with recall procedures and regulatory audits. Barcodes also bolster security by:
- Ensuring Authorized Handling: Only individuals with the right clearance can scan and handle specific items.
- Preventing Theft or Counterfeiting: Real-time tracking and record-keeping discourage unauthorized access and duplications.
This heightened accountability not only protects consumers but also safeguards brand reputation.
Commonly Used Barcode Types
Code 128
Why it’s used:
Code 128 is a high-density linear barcode capable of encoding a wide range of characters, including alphanumeric data. It’s ideal for logistics applications requiring detailed product or shipment information.
Applications:
Frequently used for tracking items in warehouses, shipping labels, and retail logistics where compactness and detail are essential.
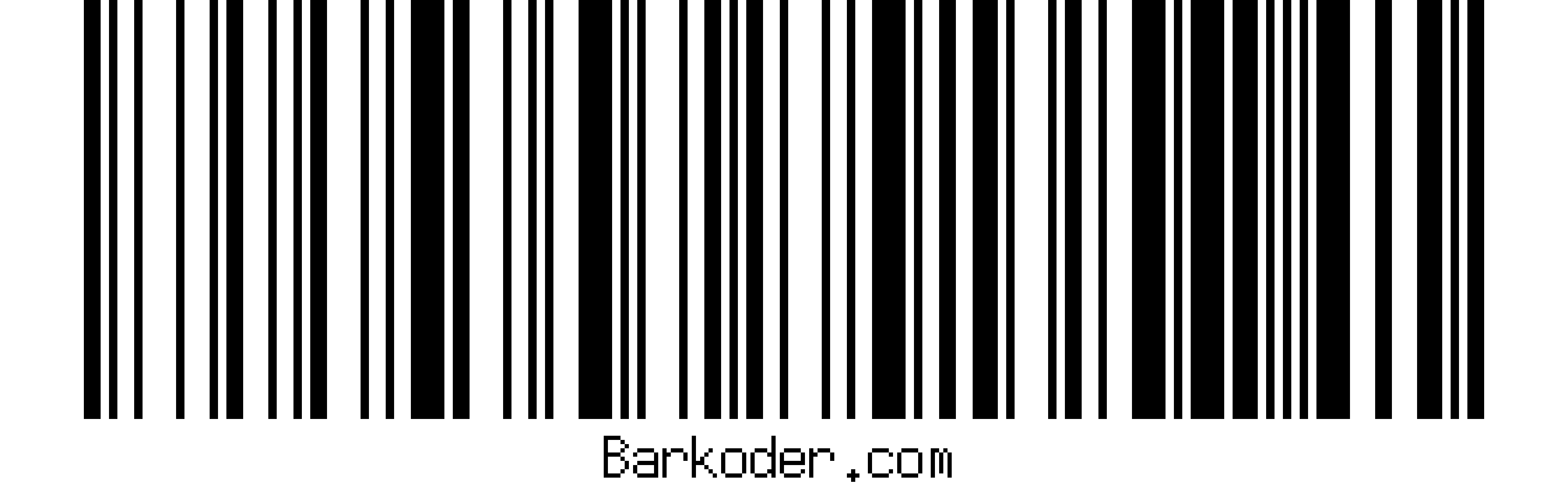
QR Code
Why it’s used:
QR Codes are 2D barcodes that store large amounts of data, including URLs and product details. They can be quickly scanned from multiple angles using scanners or smartphones, making them versatile and user-friendly.
Applications:
Commonly seen in inventory management, shipment tracking, and even customer-facing apps, providing instant access to detailed information or interactive content.
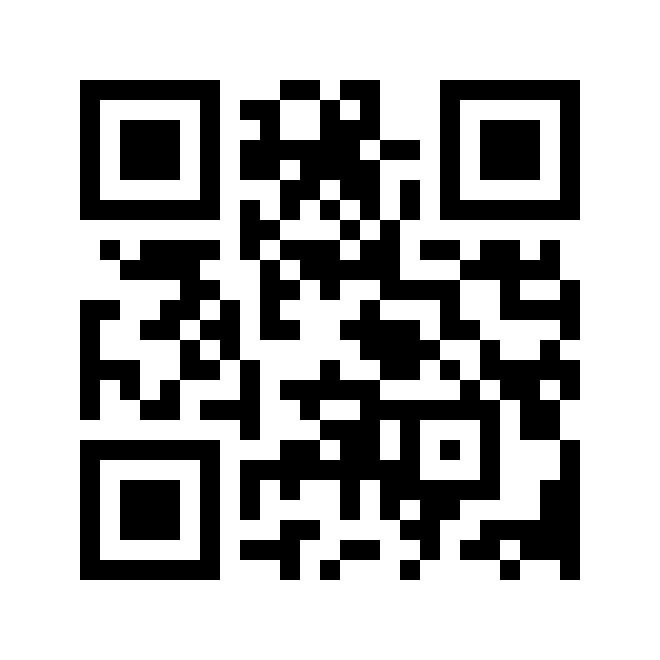
Data Matrix
Why it’s used:
Data Matrix codes are 2D barcodes known for their small size and high data capacity. They remain readable even if partially damaged, making them suitable for labeling tiny components in industries such as electronics or aerospace.
Applications:
Ideal for marking small parts and ensuring traceability where space is limited, such as on circuit boards or small product packaging.
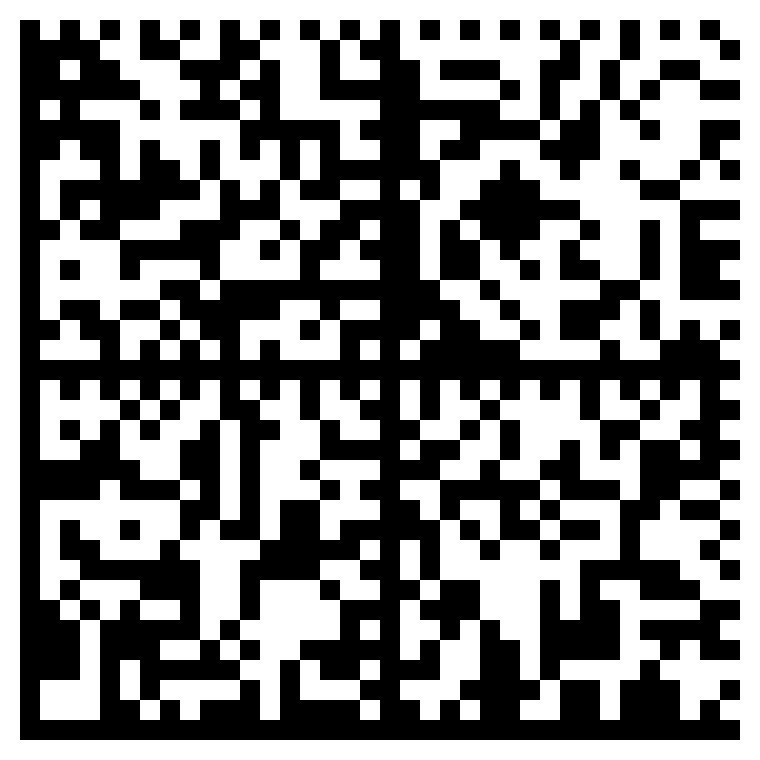
UPC (Universal Product Code)
Why it’s used:
Widely recognized in retail, UPC barcodes simplify product identification throughout the supply chain. They’re especially common for consumer goods, ensuring smooth integration with point-of-sale and warehouse systems.
Applications:
Primarily used for retail logistics and tracking consumer products from the manufacturer to the retailer.
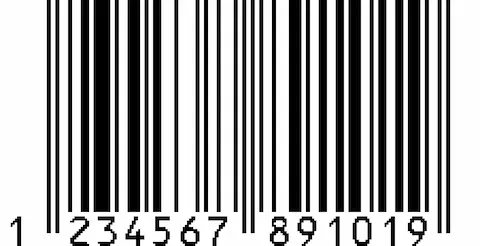
ITF-14 (Interleaved 2 of 5)
Why it’s used:
ITF-14 encodes 14-digit GTINs (Global Trade Item Numbers) and is designed to withstand rough handling on materials like corrugated cardboard. This makes it robust for warehouse and shipping environments.
Applications:
Typically used to label cases, cartons, and pallets, enabling easy scanning and tracking in distribution centers.
PDF417
Why it’s used:
PDF417 is a stacked linear barcode format capable of encoding significant amounts of data. It’s often used when detailed information—like sender/recipient details or entire shipping documents—must be stored on a single label.
Applications:
Common on shipping labels, driver’s licenses, and transportation documents, where multiple data fields need to be encoded in one compact barcode.
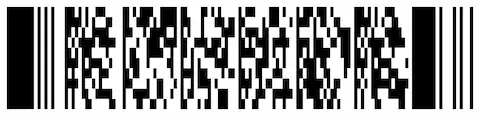
That's all nice but how can the barKoder SDK help you?
Example Use Case: barKoder in Action
Receiving Dock
- Worker scans incoming packages using a barKoder-powered mobile app.
- System validates contents against the purchase order and updates inventory levels.
Putaway
- The mobile app directs the worker to the correct shelf or bin.
- Scanning the bin’s barcode confirms where the package is stored.
Order Picking
- When an order comes in, the picking app lists items and their locations.
- Each item’s barcode is scanned upon retrieval, ensuring the correct product is picked.
Packing & Shipping
- Scans at the packing station verify correct items are grouped.
- A final scan triggers shipping updates in the system and notifies the customer.
Delivery & Returns
- At each transit checkpoint, a barcode scan logs the package’s movement.
- If a return occurs, scanning the returned product links it to the original order, streamlining reverse logistics.
Key Benefits
- Improved Accuracy: Reduces manual errors by verifying every movement of goods with a barcode scan.
- Increased Efficiency: Speeds up tasks like receiving, picking, and shipping through real-time data updates.
- Better Visibility: Creates a transparent end-to-end tracking system for every item in the supply chain.
- Lower Costs: Fewer mistakes mean less time spent correcting errors, saving on labor and reshipping expenses.
Scalable & Flexible: Deploy on existing iOS/Android devices, extend functionalities with offline scanning, and integrate seamlessly with your current systems.
As mentioned before, customers can utilize our special features like:
to maximize their ability to use barcodes within their logistics solutions.
By integrating the barKoder SDK into your logistics workflows, you can transform everyday smartphones or tablets into powerful barcode scanners. Whether you need to streamline receiving, optimize order fulfillment, or gain clearer visibility into your supply chain, barKoder’s high-performance scanning engine and flexible integration options can help your operation become more accurate, efficient, and cost-effective.