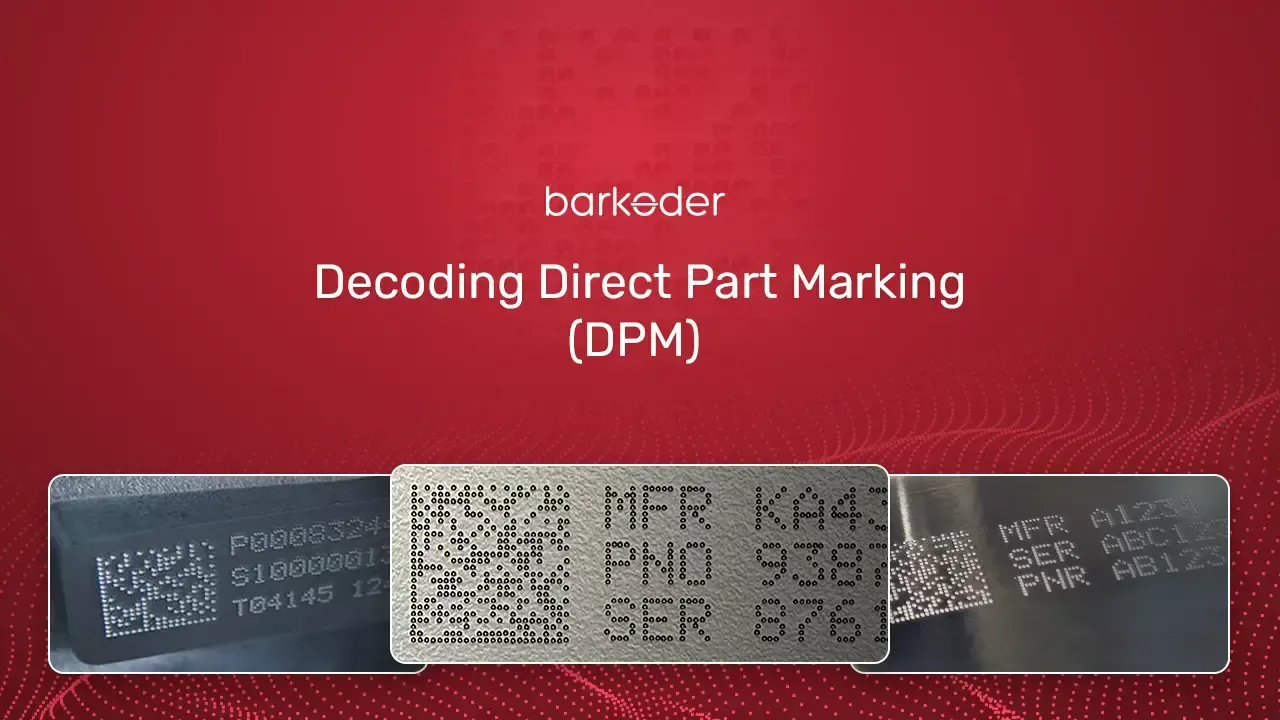
Decoding Direct Part Marking (DPM) Data Matrix Codes: An Essential Guide
In the world of modern manufacturing and tracking, Direct Part Marking (DPM) has become a crucial method for managing and identifying components, devices, and equipment. DPM involves permanently etching Data Matrix codes on various surfaces, including silicon, metal, plastic, and glass. In this article, we will delve into the significance of DPM, its common applications across industries, and the challenges it presents.
The Challenges of Scanning DPM engraved Data Matrix codes:
DPM technology plays a pivotal role in numerous industries, ensuring efficient tracking, identification, and data retrieval. Here are some of the common applications of DPM:
Color and Contrast Challenges: DPM barcodes, etched into surfaces, often lack contrast with their background. The color of the barcode matches the surface, and shadows can create variations in contrast, making decoding difficult. Additionally, imperfections in the etching process can lead to irregularly shaped dots within the barcode.
Dots Instead of Lines: DPM uses dots instead of traditional lines found in common barcodes. The spacing and shape of these dots can impact code readability. Dots that are too close or too far apart can result in decoding errors, and the irregular shape of the dots adds to the complexity.
Surface Imperfections: The quality of DPM etchings can be affected by the texture of the surface they are marked on. Surfaces may be reflective, uneven, or curved, with their own imperfections such as damage or abrasions, which can hinder the scanning process.
Challenges in Lighting: DPM barcodes are often found on curved metal surfaces and may not have ideal contrast under ambient lighting conditions. The placement of DPM barcodes in areas with poor lighting can introduce additional challenges for decoding.
Reliability in Confined Spaces: In electronic manufacturing, DPM codes can be particularly challenging due to their low contrast and tiny size, as they are directly printed on electronic components. Reliably reading such codes is crucial.
The Technology Behind DPM
DPM utilizes various technologies for permanent marking. Three main methods are widely used:
Laser Marking: Laser technology is the most popular choice for DPM. It offers high-quality marking, and high throughput, and does not require consumables. Laser marking involves altering material characteristics using different methods, such as ablation, engraving, color change, or annealing, depending on the material type.
Dot Peening: Dot peening relies on mechanical percussion to create holes in the material, which affects how light reflects on the surface, forming the barcode's dark and light elements. This method is commonly used for metal parts and is prevalent in the automotive industry.
Ink Jet Printing: Inkjet printing involves spraying ink directly onto the part's surface, creating a pattern of spots. It is versatile and can be used on various substrate materials, including plastic, metal, and glass.
DPM in Various Industries
DPM technology initially gained prominence in the automotive and mechanical industries. Still, its applications have since expanded to other sectors, including electronics, chemicals, and healthcare. It is especially valuable for applications where parts endure harsh testing processes, require continuous tracking, or involve very small items that are challenging to label. Direct Part Marking (DPM) codes, such as Data Matrix codes, QR codes, and other permanent markings on items, play a crucial role in various industries for traceability, quality control, and data management. Here's a short overview of their uses in different sectors:
- - Automotive Industry: DPM codes are widely used to mark components and parts, allowing for easy tracking throughout the supply chain. This aids in quality control, recalls, and compliance with industry standards.
- - Healthcare and Pharmaceutical: DPM codes are used on medical instruments, equipment, medication packaging and implants to ensure patient safety, track usage history, and meet regulatory requirements, as well as for authentication, tracking, and monitoring drug distribution.
- - Electronics Manufacturing and Aerospace: Manufacturers use DPM codes for process control, inventory management, and traceability of individual components. DPM codes are also employed on aircraft components for maintenance and safety purposes. They provide essential data for inspections, repairs, and ensuring the longevity of aircraft systems.
- - Food and Beverage: In this industry, DPM codes are used to mark food products and packaging for quality control, expiration tracking, and batch recalls, ensuring food safety and compliance.
- - Retail and Consumer Goods: DPM codes enable retailers to track products from production to point of sale, helping to manage inventory, reduce losses, and improve customer satisfaction.
- - Government and Defense: DPM codes are used to mark military equipment and components to ensure traceability, maintenance records, and compliance with military standards.
- - Logistics and Supply Chain: DPM codes are essential for tracking packages, pallets, and shipments across the entire supply chain, providing real-time visibility and improving logistics operations.
- - Construction and Heavy Machinery: Construction equipment and machinery often have DPM codes for maintenance scheduling, asset tracking, and optimizing usage.
In summary, DPM codes find applications in a wide range of industries for various purposes, including traceability, quality control, compliance, and data management. Their permanence and ability to store substantial information make them invaluable tools for enhancing efficiency and ensuring product and process integrity across different sectors.
Future Developments in DPM
DPM technology continues to evolve, driven by expanding use cases. As DPM codes are integrated into a broader range of industries and applications, challenges related to verification, reflectance and readability need to be addressed. The future of DPM is particularly promising with the emergence of software-based scanning solutions such as the barKoder Barcode Scanner SDK, which offer versatility and cost-efficiency compared to traditional hardware-based scanners. This shift towards software-based DPM scanners allows industries to maintain accuracy in data retrieval while managing costs effectively. Standardization of DPM quality is an ongoing process, especially as different industries continue to explore the potential of DPM technology.
In conclusion, Direct Part Marking (DPM) with Data Matrix codes has become an indispensable tool for managing components and ensuring their traceability throughout their life cycles. By understanding the technology, addressing challenges, and embracing cost-effective software-based DPM scanners such, industries can harness its potential for improved tracking, quality control, and compliance in various applications.
Below we have a brief showcasing of barKoder's newly released Enhanced DPM algorithm, hard-to-read DPM codes. This feature, already better than any alternative in the software market, is now available to mobile developers to be integrated within any Enterprise and Consumer-facing application.